. Edo shokunin 江戸職人 craftsmen, artisan, Handwerker .
:::::::::::::::::::::::::::::::::::::::::::::::::::::::::::::::::::::::::::::::::::::::::::::::::::::
Cut glass Daruma 切子だるま kiriko daruma

:::::::::::::::::::::::::::::::::::::::::::::::::::::::::::::::::::::::::::::::::::::::::::::::::::::
Edo Kiriko is a glass craft that has been handed down in Tokyo.
In Edo (present-day Tokyo) in 1824, Kyubei Kagaya started exploring the technique of cutting patterns into the surface of glass.
Edo Kiriko was fosterd in the urban culture among the townspeople, and during the Meiji era (mid-19th century), the craft introduced not only Western equipment and instruments, but also their technique while preserving traditional techniques and has been passed down to the present time.
First of all, an expert glassblower blows clear glass into a paper-thin shape of colored glass and then rotates this in the air to make the overall form. The result is a two-layer structure with colored glass on the outside and clear glass on the inside. By cutting patterns into the outside surface with different kinds of whetstones, a vivid contrast is created between the colored glass and the transparent glass.
In 1985 Edo Kiriko was designated a Traditional Craft Industry by the Tokyo Metropolitan Government.
source : web-japan.org
Edo kiriko 江戸切子

. . . CLICK here for Photos !
- quote
Edo Kiriko 江戸切子 Cut Glassware
■ Traditional Technologies and Techniques
1- Sumitsuke 墨付け (ink application) involves the use of a bamboo stick to apply ink to the surface of glassware. This preparatory process creates a basic outline of the patterns (designs) to be cut in glass.
2- Arazuri 荒摺り (rough grinding) involves the basic grinding of glass in accordance with the pattern applied to the surface using the sumitsuke process. Emery powder 金剛砂 (a grinding agent) is applied to the surface of a metal grinding wheel. This then comes into contact with the glass, and major elements of the pattern are etched accordingly. The next process 三番掛け (Sanbankake) is the application of finer grain emery powder in order to carry out more detailed pattern etching. Depending on designs, three different types of grinding wheel may be used.
3- Ishikake 石掛け (whetstone grinding) involves the use of a whetstone grinder to smooth and better define patterns etched during earlier grinding processes. Natural whetstones 丸砥石 from the southern island of Kyushu are used.
4- Kenma 研磨 (or Migaki) is the process of polishing the glass. It involves even finer-detail grinding of those surfaces that are to be non-transparent. It also brings out the traditional luster associated with transparent glass surfaces. When doing this step, polishing powder is used with a wooden polishing wheel 木車(桐、柳) (made of either Paulownia or Willow). The design is carefully polished in order to heighten both the transparency and luster of the glass.

■ Traditionally Used Raw Materials
Glass materials (crystal glass, soda lime glass)
ガラス生地(クリスタルガラス、ソーダ石灰ガラス)
■ History and Characteristics
Kiriko is a form of glass cutting in which grinders and whetstones are applied to the surface of glassware, and a number of different cutting (or grinding) techniques are employed in order to manufacture products.
The originator of the traditional craft of Edo Kiriko (cut glassware) was Kagaya Kyubei 加賀屋久兵衛, who ran a glassware store in Edo's Odenmacho 大伝馬町 (in the vicinity of modern Nihonbashi).
Kyubei is said to have learned his craft in Osaka, which at one stage was a leading center of glassware production in Japan. After completion of his apprenticeship, he returned to Edo and opened a glassware store in the city, where items such as eye glasses, thermometers and hydrometers were produced.
Edo Kiriko techniques deliver exquisite patterns that are both sparkling and lustrous when applied to suitable glassware such as "crystal glass," such techniques delivering products of great intrinsic value.
As Japan moved from the Taisho Era to the Showa Era, manufacturing evolved so quickly that "cut glass" came to be synonymous with "artistic glass," with the industry reaching its pre-war zenith around 1940.
In contemporary times, approximately 80% of Edo Kiriko manufacturing occurs in Koto and Sumida Wards.
Concerning Satsuma Kiriko 薩摩切子 (cut glassware produced in Kyushu), which is as equally loved as Edo Kiriko, it resulted from the Satsuma Domain (who ruled over modern Kagoshima Prefecture) inviting the Edo glassware manufacturer, Yotsumoto Kamejiro 四本亀次郎, to establish glassware production in the domain. This industry grew quickly as the government of Satsuma fully supported its development.
Tokyo Cut Glass Manufacturing Cooperative Association
- source : www.sangyo-rodo.metro.tokyo.jp
.............................................................................
- quote
Edo Garasu 江戸硝子 Edo Glassware
■ Traditional Technologies and Techniques
1- Glassblowing 吹きガラス:
Molten glass is spooled at the end of a blowpipe and air is blown in by mouth to shape the glass.
① Free-blowing 宙吹き:
Glass is spooled at the end of a blowpipe, air is blown into the molten glass as it is held in the air and rotated. Tweezers and other tools are used to make adjustments to the shape. The workpiece is heated in the furnace as shaping operations are repeated.
② Mold-blowing 型吹き:
In addition to the steps followed in free-blowing, a wooden or metal mold is used to shape the glass.
2- Pressed glass 型押し:
A plunger (male section) and a mold (female section) are created 雄雌の両型. Glass is spooled at the end of a blowpipe and inserted into the mold. The plunger is used to press the glass into the mold and shape it.

■ Traditionally Used Raw Materials
Silica sand, sodium carbonate, lime, potash, lead oxide, etc.
珪砂、ソーダ灰、石灰、カリ、酸化鉛等
■ History and Characteristics
1. Glass production in Japan
Glass production began in Japan during the Yayoi Period (300 BCE-300 CE). Production was discontinued for a time from the Heian Period (794-1185) to the Muromachi Period (1338-1573), before being revived following the importation of glassmaking technologies from China, Portugal and the Netherlands in the 16th and 17th centuries. Former names for glass in Japanese (currently garasu or shoshi) include ruri 瑠璃, a Japanese form of lapis lazuli; hari はり from the Chinese word boli; biidoro ビードロ from the Portuguese word vidro; and giyaman ギヤマン from the Dutch word diamant. These names also provide evidence of the overseas links that glass production in Japan enjoys.
2. Glass production in Edo (Tokyo)
Glass production in Edo is said to have started at the beginning of the 18th century, with items such as mirrors and eyeglasses produced by the first Kagaya (Minagawa) Kyubei 加賀屋(皆川)久兵衛 in the Nihonbashi-Torishiocho neighborhood. Ornamental hairpins and wind chimes were also produced by Kazusaya Tomesaburo 上総屋留三郎 in the Asakusa neighborhood. The names of Kagaya Kyubei and his son Kumasaki Yasutaro 熊崎安太郎 are included in the catalog of exhibits for Japan's First National Industrial Exhibition in 1877.
3. Cooperative association of glass producers
The Tokyo Glass [Hari] Producers Association 東京はり製造人組合 was founded in 1879. It underwent many changes over time, leading eventually to the establishment of the TOBU Glass Industry Co-operative Association of Japan (TGIA) 社団法人東部硝子工業会 in 1949. The aim of TGIA is to promote friendship, information exchange, communication and coordination among members.
4. Characteristics
Modern glass production was brought to Edo after first passing through Nagasaki, Osaka and Kyoto. In addition to items such as dishware for everyday use and bottles/jars, scientific instruments such as thermometers and hydrometers were made in response to orders from the scholar and politician Sakuma Shozan 佐久間象山 (1811-1864) as well as other people. During the early Meiji Period, glassmaking developed into one of Tokyo's local industries as modern European methods were integrated and the industry grew to meet a wide range of needs.
Glassware Manufacturing Association
- source : www.sangyo-rodo.metro.tokyo.jp
.............................................................................


source : tdehdajez.cocolog-nifty.com
カガミクリスタル 江戸切子 This apple comes in green, blue and other colors.
. Welcome to Edo 江戸 ! .
.................................................................................
quote
Brilliant facets of Nishi-Ojima
By KIT NAGAMURA
I'm delighted to find the workshop of Toshio Takizawa, master craftsman of Edo Kiriko, a Japanese style of cut and faceted glass said to date from 1834. The most popular form now features crystal or clear glass coated with a colored layer on the outside, through which the artisan engraves and facets geometric or freehand designs. Takizawa invites me in, saying, "I entertain visitors and media all the time."
... the Ojima area was once crisscrossed by canals for barges transporting glass and coal. "A lot of glasswork is noisy, and when ordinary residents settled here, they complained about that," he says. "But Edo Kiriko work is relatively quiet, so there are a few of us still around."
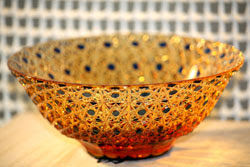
source : Japan Times, 2011
:::::::::::::::::::::::::::::::::::::::::::::::::::::::::::::::::::::::::::::::::::::::::::::::::::::
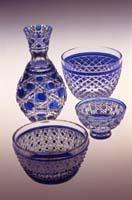
寒造透かせグラスの江戸切子
kanzukuri sukase-gurasu no Edo kiriko
ricewine brewed in the cold -
a transparent glass of
old Edo cut glass
吉岡ゆたか Yoshioka Yutaka
www5.ocn.ne.jp/~turu/kukai/g_200503.html
click on the photo for more about rice wine
:::::::::::::::::::::::::::::::::::::::::::::::::::::::::::::::::::::::::::::::::::::::::::::::::::::
Satsuma Kiriko
is a traditional glass handicraft, made in Kagoshima prefecture, Japan.
Real Satsuma Kiriko is extremely expesive and rare, because Satsuma kingdom made this glass handicraft, only less than twenty years at the end of Edo Period.
Satsuma kingdom is the leading player of Meiji modern revolution, so Japanese people feel the all the romance of Japan's modernization in Satsuma Kiriko.
In recent decades, from 1985, Satsuma Kiriko started to be reproduced by its descendants.
source : stores.japanesegoods.jp
Satsuma kiriko 薩摩切子
. . . CLICK here for Photos !
:::::::::::::::::::::::::::::::::::::::::::::::::::::::::::::::::::::::::::::::::::::::::::::::::::::
Ryuukyuu garasu 琉球硝子 Ryukyu glassware

琉球ガラス村 Ryukyu Glass Village
- reference source : ryukyu-glass.co.jp -
- quote -
Ryukyu Glass
Some say the sea in Okinawa is rainbow colored. In fact, the sea around the southern islands has many colors: deep blue, sky blue, emerald green, orange and yellow at sunrise and sunset etc. Ryukyu Glass may have inherited its qualities from the colorful and calm sea of Okinawa.
Glassware was originally brought to Okinawa from Southeast Asia and the Strait of Malacca several centuries ago. However, its production did not begin until the 19th century. Glassware was easily broken during the long ship voyages from overseas, which led the people of Okinawa to invite glass craftsmen from Nagasaki or Osaka to their land so they could learn how to make medicine bottles and lamps for themselves. They also used all kinds of recycled glass, like broken glass pieces from foreign ships, used sake and soy sauce bottles. They also made use of inferior products like air bubbled or unevenly thickened glass. These factors all contributed to the unique design of Ryukyu glass.
In 1972, the Okinawa Ocean Expo was held, igniting tourism in Okinawa.
The more tourists visited the islands, the more souvenirs were sold. In response to these happenings, local glassmakers started expanding their industry; they introduced new glass materials in addition to the traditional recycled glass, and developed new techniques for coloring. In 1998, Ryukyu Glass was registered as one of the Traditional Crafts of Japan. There are many glassmakers in Okinawa producing many kinds of glassware, from artistic pieces to gift items.
Ryukyu glass reflects the values of Okinawa:
Don’t waste, recycle. Be flexible and adaptable.
And most importantly, every imperfection is useful.
- source : Japan Brand 109 -

. Ryuukyuu 琉球 Ryukyu art and craft, Okinawa .
:::::::::::::::::::::::::::::::::::::::::::::::::::::::::::::::::::::::::::::::::::::::::::::::::::
. Tsugaru Glas 津軽のガラス工芸 - Aomori .
. Hagi 萩のガラス工芸 glass art from Hagi . - Yamaguchi
. Matsugaoka Glass Products / 松ヶ岡ガラス工業 - Yamagata .
. mamezara 豆皿 small plates "beans size" .
:::::::::::::::::::::::::::::::::::::::::::::::::::::::::::::::::::::::::::::::::::::::::::::::::::
kiriko mandala 切子曼陀羅



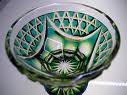
:::::::::::::::::::::::::::::::::::::::::::::::::::::::::::::::::::::::::::::::::::::::::::::::::::::
kigo for all summer
kiriko 切子(きりこ)cut glass
..... kattogurasu カットグラス
..... gyaman ギヤマン (diamant)
..... biidoro びいどろ (vidro)
.SAIJIKI ... HUMANITY - Kigo for Summer
.......................................................................
. biidoro ビードロ vidro
hoppen ぽっぺん glass ball plopping
kigo for the New Year
biidoroya, biidoro-ya 硝子屋 craftsman making glass ware
garasu ku 硝子工 glass blowers
gyaman ギャマン = diamond ダイアモンド

source : edomono.tumblr.com
Making glass items had been introduced in the Heian period, but was soon forgotten.
In the middle of the Edo period, things made of glass have become quite popular, from Kanzashi hairpins to cups and plates.
All the glass items were blown from a round piece (tama 玉). It was then blown into shape.
An old saying goes:
tamatori san nen, kiji hachi nen 玉取り三年 素地八年
making the right glass ball takes three years
making the right form out of it takes eight years
Popen o fuku musume ポペンを吹く娘 Girl blowing a "Poppen" glass
ビイドロを吹く娘 / ポピン popin
. 喜多川歌麿 Kitagawa Utamaro .
:::::::::::::::::::::::::::::::::::::::::::::::::::::::::::::::::::::::::::::::::::::::::::::::::::::::

source : item.rakuten.co.jp/plywood
. Fuji San 富士山 Mount Fuji .
:::::::::::::::::::::::::::::::::::::::::::::::::::::::::::::::::::::::::::::::::::::::::::::::::::::

source : karen of facebook 2018
Hoya Crystal
:::::::::::::::::::::::::::::::::::::::::::::::::::::::::::::::::::::::::::::::::::::::::::::::::::::::
. Edo shokunin 江戸職人 craftsmen - ABC list .
[ . BACK to DARUMA MUSEUM TOP . ]
[ . BACK to WORLDKIGO . TOP . ]
- #kiriki #glassware #ryukyuglass -
:::::::::::::::::::::::::::::::::::::::::::::::::::::::::::::::::::::::::::::::::::::::::::::::::::::::
8 comments:
Beautiful haiku!
these are stunningly beautiful!!!
Doreen
beautiful! thanks for sharing!
blessings,
stacy :-)
mandala oasis
Wonderful glass pieces Gabi.
G.
These are exquisite!
just beautiful... Thanks for sharing these treasures with
us Gabi!
Mandala Oasis
Very nice!
Thank you so much to sharing!
Annalisa
Scientists: Glass dish unearthed in Nara came from Roman Empire
A glass dish unearthed from a burial mound here is the first of its kind confirmed to have come to Japan from the Roman Empire, a research team said.
A round cut glass bowl, discovered with the glass plate, was found to have originated in Sassanid Persia (226-651), the researchers said.
The dish and bowl were retrieved together from the No. 126 tumulus of the Niizawa Senzuka cluster of ancient graves, a national historic site. The No. 126 tumulus dates back to the late fifth century.
The researchers’ scientific studies show that fifth-century Japan imported glasswork, and that there was a wide range of trade between the East and the West.
“The dish was likely produced around the Mediterranean Sea and then transferred to Sassanid Persia,” said team leader Yoshinari Abe, an assistant professor of analytical chemistry at the Tokyo University of Science. “After it was painted there, the plate was probably taken to Japan.”
According to the team’s analysis, the chemical composition of the clear dark blue dish is almost identical to glasswork unearthed in the area of the Roman Empire (27 B.C.-A.D. 395).
Measuring 14.1 to 14.5 centimeters in diameter, the flat, raised dish is believed to have been created in the second century at the latest.
The dish has been designated a national important cultural property and is currently owned by the Tokyo National Museum.
continue
http://ajw.asahi.com/article/behind_news/social_affairs/AJ201411130064
.
A history of glass in Japan
Dorothy Blair, Corning Museum of Glass
.
at google books .
Post a Comment